Cogenerazione
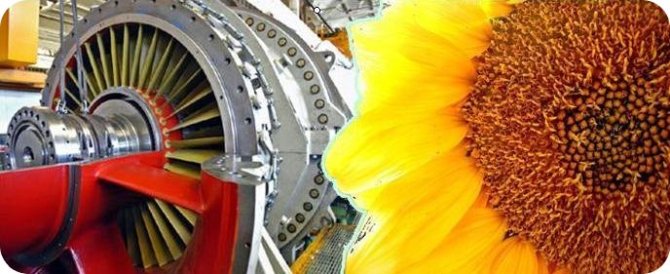
Col termine cogenerazione si indica la produzione contemporanea di diverse forme di energia secondaria (energia elettrica e/o meccanica ed energia termica) partendo da un'unica fonte (sia fossile che rinnovabile) attuata in un unico sistema integrato.
Un esempio classico è dato dal funzionamento di un'automobile, la potenza prelevata dall'albero motore è usata per la trazione e la produzione di elettricità, il calore sottratto ai cilindri per il riscaldamento dell'abitacolo e la pressione dei gas di scarico per muovere la turbina di sovralimentazione. Lo sfruttamento di calore e pressione non comporta un aumento dei consumi poiché sono "scarti" del processo di conversione da energia chimica ad energia meccanica attuato dal motore.
Il loro sfruttamento consente a parità di energia primaria immessa (il combustibile) una maggiore quantità di energia secondaria prodotta (movimento, calore). Un sistema che opera la cogenerazione è il cosiddetto co-generatore.
Uno dei primi esempi di diffusione della cogenerazione su piccola scala in Italia è stato il TOTEM realizzato nel 1973 dall'ing. Palazzetti, del centro ricerche FIAT.
Impieghi della cogenerazione
L'energia termica può essere utilizzata per uso industriale o condizionamento ambientale: riscaldamento e raffreddamento.
La cogenerazione viene realizzata in particolari centrali termoelettriche, dove si recuperano l'acqua calda o il vapore di processo e/o i fumi, prodotti da un motore primo alimentato a combustibile fossile (gas naturale, olio combustibile, biomasse, etc): si ottiene così un significativo risparmio di energia rispetto alla produzione separata dell'energia elettrica (tramite generazione in centrale elettrica) e dell'energia termica (tramite centrale termica tradizionale).
Tipologie di impianti cogenerativi
Il più comune esempio di impianto cogenerativo è quello realizzato con turbogas/motore alternativo e caldaia a recupero. I fumi del turbogas o del motore alternativo vengono convogliati attraverso un condotto fumi nella caldaia a recupero. I fumi in caldaia permettono di produrre acqua calda, vapore saturo o vapore surriscaldato. Solitamente si utilizza acqua calda per scopi di riscaldamento, vapore saturo per utenze industriali e vapore surriscaldato per turbine a vapore e utenze. In definitiva si ha produzione di energia elettrica attraverso l'alternatore accoppiato al turbogas/motore alternativo ed eventualmente attraverso l'alternatore accoppiato a1 turbovapore e produzione di energia termica sotto forma di vapore, sfruttato poi dalle utenze connesse. Per quanto riguarda i motori a combustione interna, generalmente solo il 33% dell’energia termica totalmente disponibile viene trasformata in energia meccanica. La restante è in parte perduta causa irreversibilità presenti nel motore pari ad un altro33% dell’energia totale ed infine l’ultimo 33% viene emessa nell’ambiente esterno sotto forma di energia termica che va in definitiva perduta. Per recuperare tale calore altrimenti perduto si utilizzano diversi scambiatori di calore:
un primo scambiatore, che permette il raffreddamento dell'olio lubrificante, è disponibile a bassa temperatura (non oltre gli 80°C);
un altro scambiatore per il raffreddamento dell’acqua destinata a refrigerare il motore stesso;
ed infine un ultimo scambiatore posto allo scarico del motore che permette di innalzare di molto la temperatura del fluido di scambio termico, che generalmente è acqua e che per questo ulteriore scambio termico arriva allo stato di vapore surriscaldato. Attraverso tali impianti è possibile produrre energia elettrica o termica.
Infine, fluidi evolventi particolarmente usati sono gli olii diatermici derivati dal petrolio, che hanno la caratteristica di mantenersi liquidi a pressione atmosferica fino a temperature di 300° celsius, ed hanno un punto di solidificazione molto inferiore rispetto all'acqua, cosa che impedisce che gelino nelle condotte.